Formed NISSO Equipment Maintenance Unit
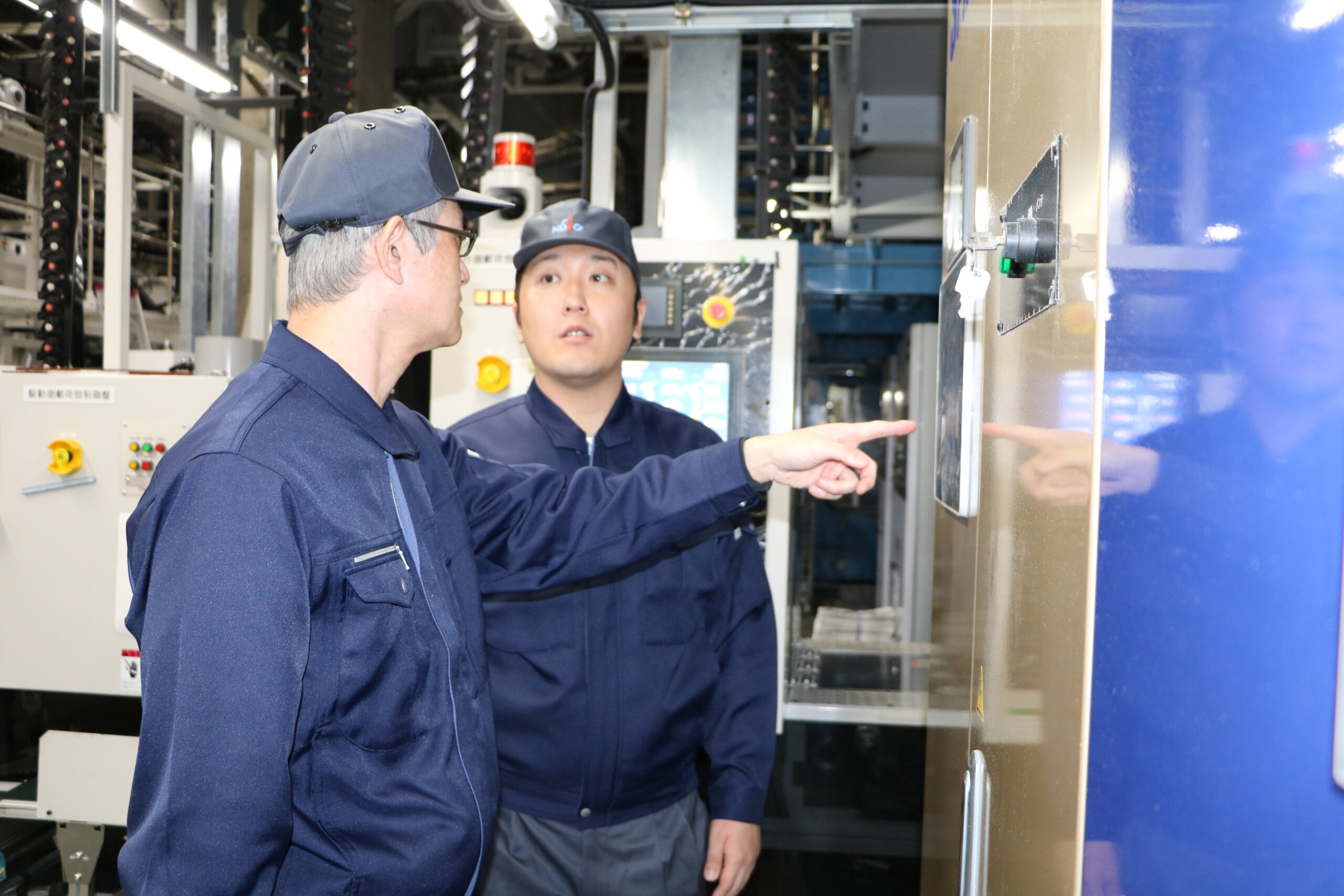
This is a customer case of a semiconductor manufacturer.In conjunction with the launch of a new plant, we established a system to perform all semiconductor equipment maintenance work for the production line.
Customer Concerns
- 課題01
- To facilitate information linkage, we would like to have all semiconductor equipment maintenance work for the production line performed in one place.
- 課題02
- I want to see a system in place to achieve improvement activities and to work with a high level of control.
Effects of Service Introduction
- 効果01
- Established a system of batch operations, including training and assigning 200 people in one year.
- 効果02
- High cost performance by managing productivity with our unique know-how
We were able to systematically assign engineers who had been trained and developed at the Nisso Technical Center.After assignment, regular meetings were held with the customer to correct errors and maintain a high attendance and retention rate of 98%, and the customer's goals of 100% proficiency and utilization rate were achieved.
"We were able to demonstrate not only direct labor cost reduction, but also indirect labor cost reduction by implementing a service with a leader.
We were also able to demonstrate high cost performance through increased productivity by achieving our proficiency rate and utilization rate goals."
Related services in this case study
※ You will be redirected to a form for downloading materials.
We will send you the URL of the document download page to the e-mail address you provide.