Detecting abnormalities in product defects by introducing AI
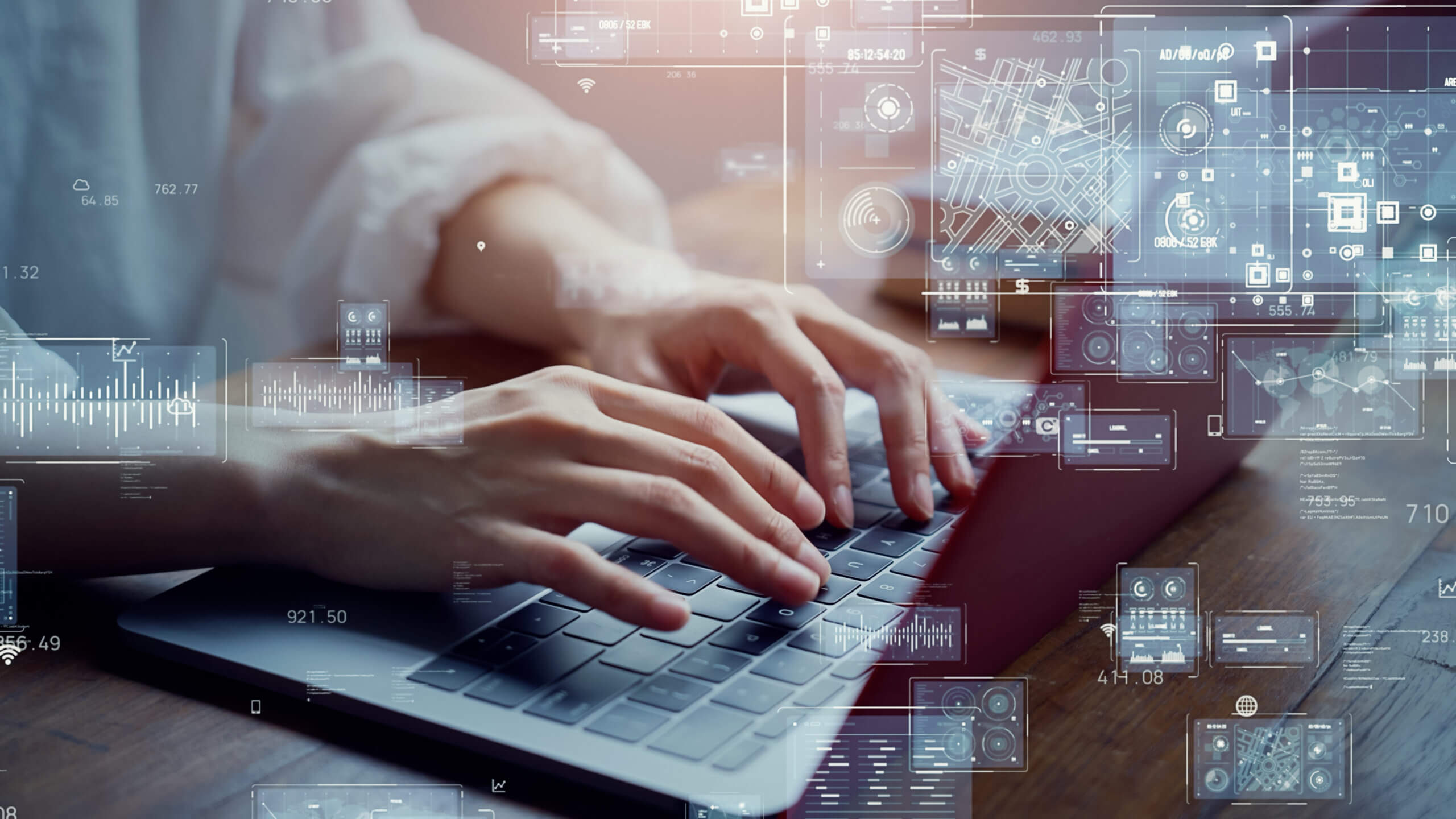
This is a case study of a customer who is a manufacturer of manufacturing equipment.AI was introduced to the work that used to be performed by a product visual inspection machine to inspect all the products. Zero defective products were missed and less than 3% of products were over-detected, thus reducing the number of inspectors.
Customer Concerns
- 課題01
- Visual inspection work is difficult and inspectors are not retained.
- 課題02
- The inspection process is being automated, but there are many over-detections.
- 課題03
- Lack of expertise and inability to take the plunge into AI implementation
Effects of Service Introduction
- 効果01
- AI tools specialized for the image domain enable highly accurate detection of defective products.
- 効果02
- Suppresses over-detection of quality and gray areas where it is difficult to determine good or bad
- 効果03
- Reduced manpower requirements for secondary inspection personnel
Eliminates defective products from being passed on to subsequent processes by eliminating the possibility of missing defective products.By controlling over-detection, the number of secondary inspection personnel has been reduced. In addition, even inexperienced employees can now easily make good/fail judgments, and the lower level of difficulty in the work has improved the retention rate. The company was also able to achieve benefits in terms of human resource development and technology transfer.
What is NISSO KOSAN's AI solution service?
NISSO's AI Solution Service provides support from the development of the imaging environment to image data processing (annotation) and AI implementation through the assignment of specialized engineers.
Related services in this case study
※ You will be redirected to a form for downloading materials.
We will send you the URL of the document download page to the e-mail address you provide.