Predictive Maintenance AI learns from vibration data.Various cost improvements
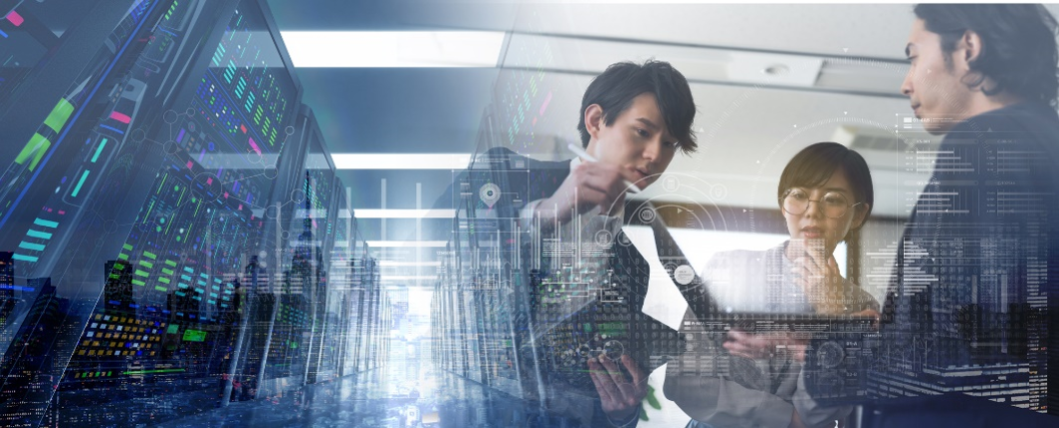
This is a customer case study of a parts manufacturer.Data was extracted from manufacturing equipment and predictive maintenance AI was utilized. The customer was able to reduce sales loss and maintenance costs by shortening downtime, while reducing various costs that had been incurred due to inadequate prediction of breakdowns.
Customer Concerns
- 課題01
- Failure of manufacturing equipment was restored by after-the-fact maintenance, resulting in operational losses.
- 課題02
- Product defects were occurring due to deterioration and failure of consumable parts of manufacturing equipment.
- 課題03
- When performing predictive maintenance on manufacturing equipment, failure data is often not available.
Effects of Service Introduction
- 効果01
- Operational losses due to sudden breakdowns of manufacturing equipment were reduced.
- 効果02
- Reduced product defects
- 効果03
- Maintenance plans could be developed by identifying the replacement cycle of consumables, etc.
By utilizing predictive maintenance AI, it is now possible to reduce sales loss and maintenance costs by shortening downtime, as opposed to the various costs incurred in the past when failures could not be adequately predicted.
NISSO's AI Solution Service provides support from the extraction of data from manufacturing equipment, data organization, data analysis, and implementation of AI predictive maintenance, after our expert engineers confirm the customer's needs.
Related services in this case study
※ You will be redirected to a form for downloading materials.
We will send you the URL of the document download page to the e-mail address you provide.